When people talk about milk powder, they often think of the healthy growth of babies and the endless care of mothers. However, few people know that a seemingly insignificant technology is quietly playing an important role in the production of milk powder, which is the peristaltic pump. Through its excellent performance and wide application, peristaltic pump has become an indispensable force in the production of milk powder in the field of spray drying.
So how is milk powder made?
The production process of milk powder can be divided into two types: dry method and wet method. The uniformity of products using dry process is poor, and currently the mainstream international production method for milk powder is wet process.
After homogenization, heating, and vacuum concentration, milk becomes concentrated milk. The milk powder is delivered to the spray drying equipment via the peristaltic pump, dehydrated into powder, cooled quickly and screened, and then the production of milk powder is completed.
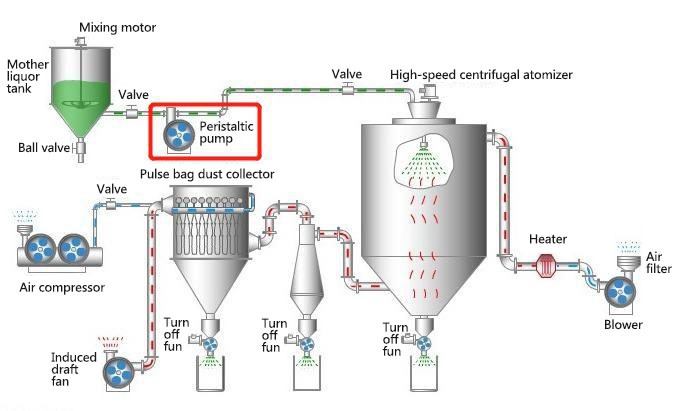
Application of Lead Fluid peristaltic pump in spray drying equipment
The spray drying equipment can dry the configured raw materials into powder, granule, hollow ball or agglomerate. Currently widely used in industries such as food and medicine.
Working principle of spray drying equipment
Use spray method to spray materials into droplets and disperse them in hot air. Materials and hot air contact each other in parallel, countercurrent or mixed flow, so that water can evaporate quickly and achieve the purpose of drying.
Compared with the dry production process, the spray drying equipment can save unit operations such as filtering and crushing, which is short in time, high in efficiency, and can avoid secondary pollution.
Early pain points of spray drying equipment
In the early stage of fluid transmission of spray drying equipment, gear pump or plunger pump are mostly used, but there are many pain points in the application of these two pumps: when handling high concentration milk powder solution, it may cause temperature rise, bubble generation, or even poor dehydration effect. These issues not only affect the quality of milk powder, but may also lead to energy waste and reduced production efficiency.
1.Cleanliness requirements: The structure of gear pumps and plunger pumps is complex, causing liquid to easily remain in the pump body, which is not suitable for high cleanliness requirements in production.
2.Maintenance cost: The gears of the gear pump are prone to wear and tear, requiring regular maintenance and replacement; The plunger pump has a complex structure and high requirements for conveying medium, as well as high costs for use and maintenance.
Peristaltic pump assisted spray drying equipment
Peristaltic pumps have multiple advantages and can perfectly replace gear pumps or plunger pumps.
1.High cleanliness: The peristaltic pump only contacts the pump tubeand does not contact the pump body for fluid transmission. The tubemeet cleanliness certification standards such as GMP, USP Class VI, FDA, and NSF, with high cleanliness.
2.Simple maintenance: The peristaltic pump has a simple structure and no components such as valves and seals. Simply replace the peristaltic pump tubeand it can be used continuously for over 500 hours, and the replacement of the tubecan be completed in less than 1 minute. Simple and convenient, with lower costs.
3.Higher accuracy: The volume pumped by the peristaltic pump is constant every revolution, so the peristaltic pump can achieve high accuracy and stability, and the flow rate is easy to adjust.
The peristaltic pump perfectly meets the application requirements of spray drying equipment in many aspects, helping spray drying equipment work with high quality and efficiency.