Throughout history, industrial explosion accidents have loomed over human development like a dark cloud. From the devastating explosion in Halifax, Canada, in 1917, which almost destroyed the entire city, to the gas leak at the Bhopal pesticide plant in India in 1984, and the catastrophic explosion at the Xiangshui Chemical Plant in Jiangsu, China, in 2019, each incident has sounded a painful alarm about safety.
Today, we learn from history and build stronger explosion-proof safety defenses through active technological innovation and strict safety management, ensuring that past tragedies do not become future reenactments.
PART 01
Definition of Explosion-Proof
Explosion-proof, as the name implies, is to prevent explosions. In the industrial field, explosion-proof specifically refers to the state or ability of equipment or systems to resist the impact and heat of an explosion without damage and continue to function normally. Its core lies in preventing explosive mixtures (gases, vapors, dust, etc.) from being ignited or detonated in specific environments and limiting the spread and destructive power of explosions.
Globally, countries and regions have established corresponding explosion-proof standards and certification systems, such as the IECEx certification of the International Electrotechnical Commission, OSHA, NFPA, ASTM in the United States, and the ATEX directive and EN series standards in Europe. In China, the GB/T 3836 series of national standards provide authoritative guidance for explosion-proof work and are continuously updated and improved.
PART 02
How Explosions Occur
For an explosion to occur, certain preconditions must be met: the presence of flammable materials, sufficient oxidizing agents (usually oxygen, within the explosive limit range), and an ignition source (with energy greater than the minimum ignition energy of the flammable mixture). An explosion can occur only when these three factors coexist in a certain area.
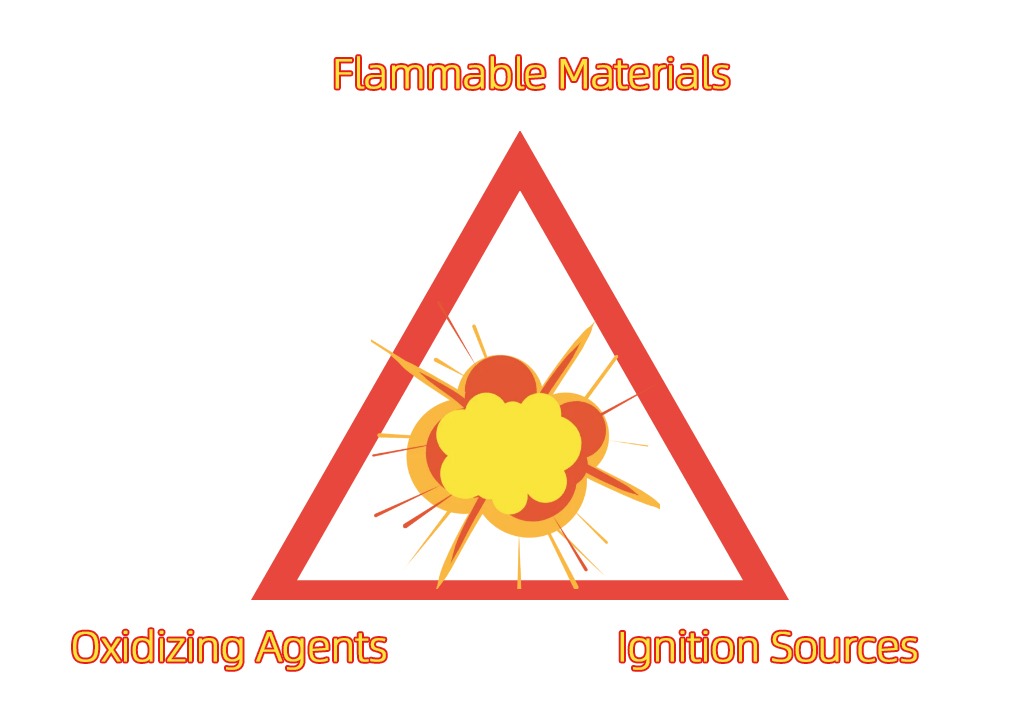
- Flammable materials: gases, liquids, and solid substances that can react with oxygen.
- Oxidizing agents: mainly oxygen.
- Ignition sources: open flames, electrical sparks, mechanical friction, static discharge, high-temperature surfaces, energy from chemical reactions, and light energy.
Based on these causes, explosion-proof measures involve controlling or eliminating one or more of these factors to prevent explosions:
1. Avoid forming explosive environments.
2. Eliminate possible ignition sources.
3. Control the hazards of explosions.
PART 03
Understanding Explosive Environments
An explosive environment is one where a mixture of flammable substances and air reaches a certain concentration under atmospheric conditions, and sufficient ignition sources can cause explosions.
Fields with potential explosion hazards:
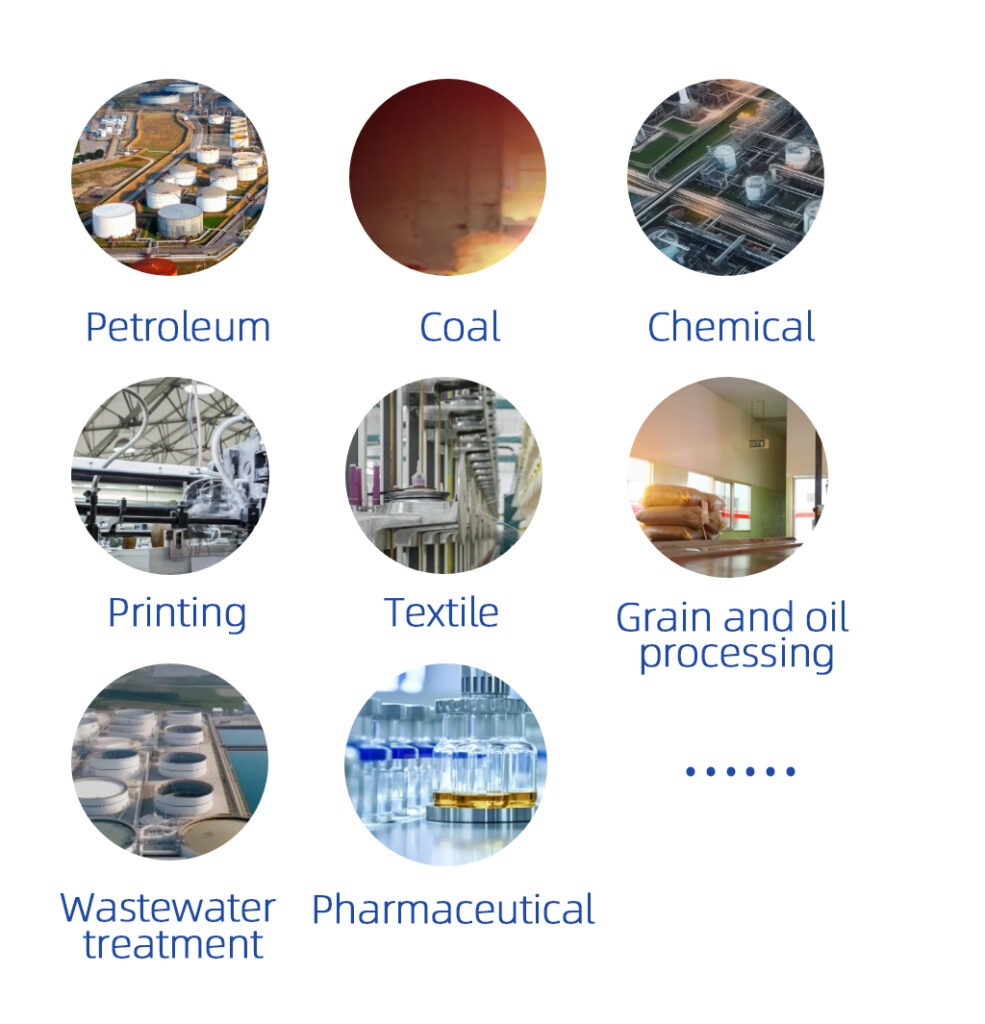
The GB/T 3836 series standards classify explosive environments into explosive gas atmospheres and explosive dust atmospheres based on the different forms of flammable substances and the characteristics of explosive environments:
1.Explosive gas atmosphere:an environment where a mixture of gases, vapors, or mist-like flammable substances and air ignites, and the combustion spreads to all unburned mixtures. Zone 0, Zone 1, Zone 2 based on the frequency and duration of the explosive gas atmosphere.
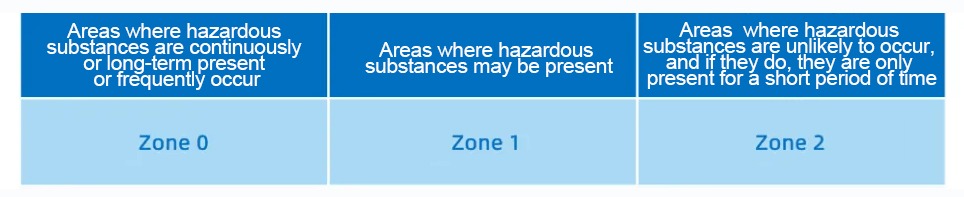
2. Explosive dust atmosphere:an environment where a mixture of dust or fibrous flammable substances and air ignites, and the combustion spreads to all unburned mixtures. Zone 20, Zone 21, Zone 22 based on the frequency and duration of the explosive dust mixture.
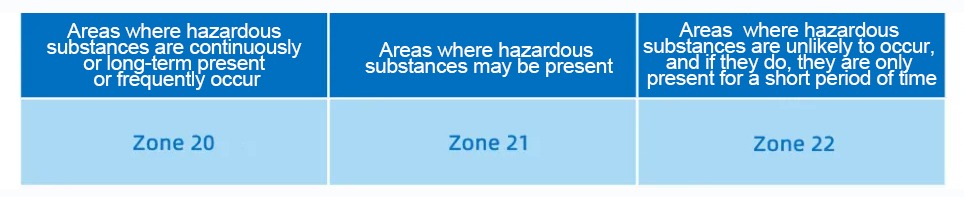
These classifications help determine applicable explosion-proof standards and equipment selection.
PART 04
Classification of Explosive Substances
In China, explosive substances are classified into three categories based on the energy required for spark ignition:
Category I: Methane in coal mines.
Category II: Explosive gas mixtures.
Category III: Flammable dust/fibers.
Category II is further divided into IIA, IIB, and IIC, and Category III into IIIA, IIIB, and IIIC.
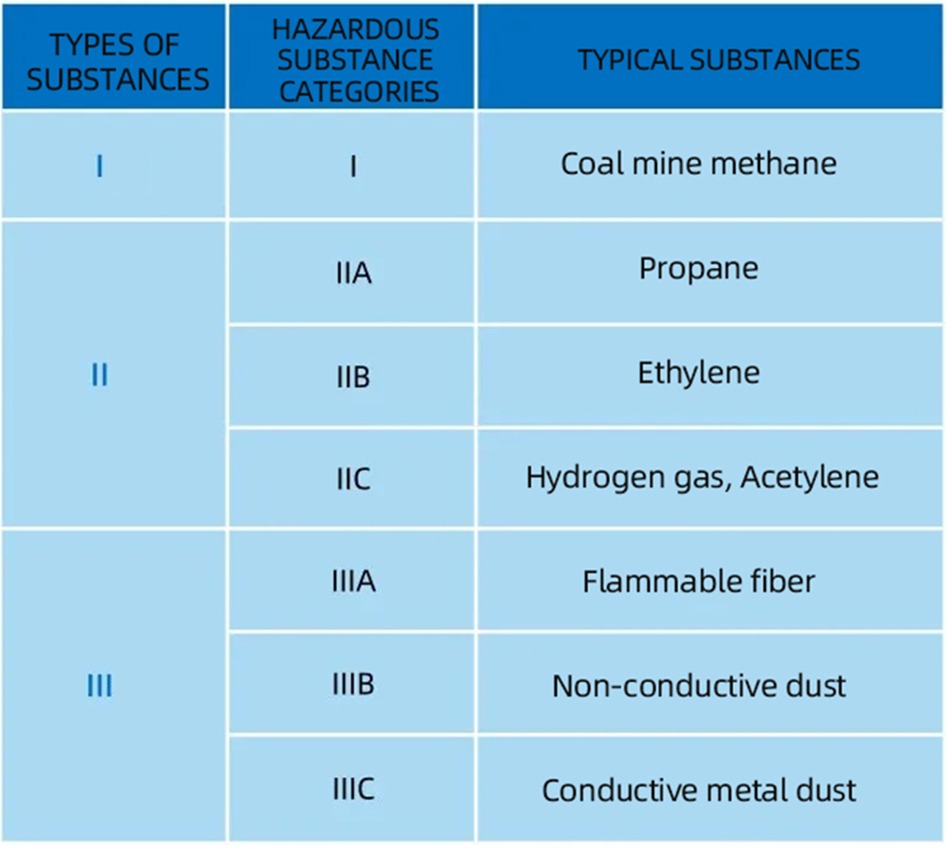
The most hazardous substances in each category are IIC and IIIC.
PART 05
High Temperature – A Potential Ignition Source Not to Be Ignored
High temperatures are potential ignition sources that cannot be ignored. Besides common ignition sources like sparks and open flames, equipment or system surfaces reaching specific threshold temperatures can also ignite explosive mixtures.
To manage this risk effectively, international and domestic explosion-proof standards introduce the concept of temperature classes marked from T1 to T6, detailing the highest allowable surface temperatures for equipment or systems.
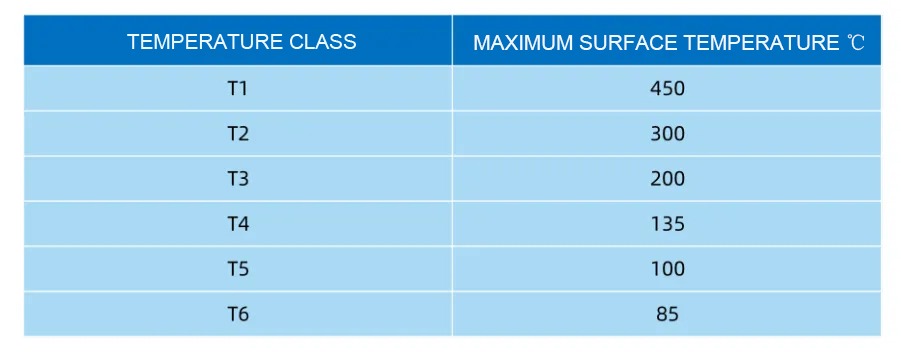
The maximum surface temperature refers to the highest temperature reached by any part or surface of electrical equipment when operating under the most unfavorable conditions (but within the specified permissible range).
PART 06
Introduction to Explosion-Proof Markings
Explosion-proof markings or certificates act as an ID for explosion-proof products. They inform us about the explosion-proof forms, applicable environments, and zones of the equipment.
Taking Lead Fluid EF900 and EF800 series products’ explosion-proof certificates as examples:
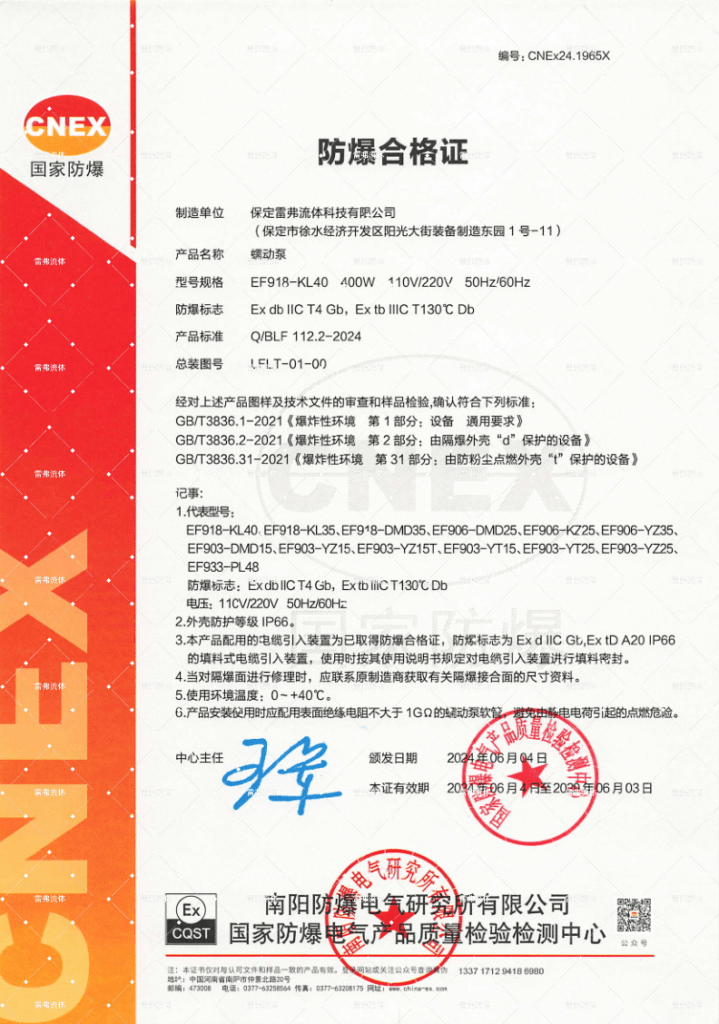
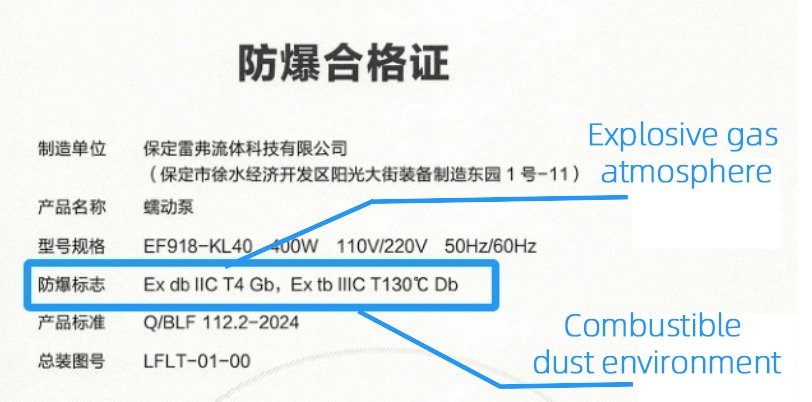
The explosion-proof marking is divided into two parts: the part before the comma pertains to explosive gas environments, and the part after the comma pertains to flammable gas atmosphere.
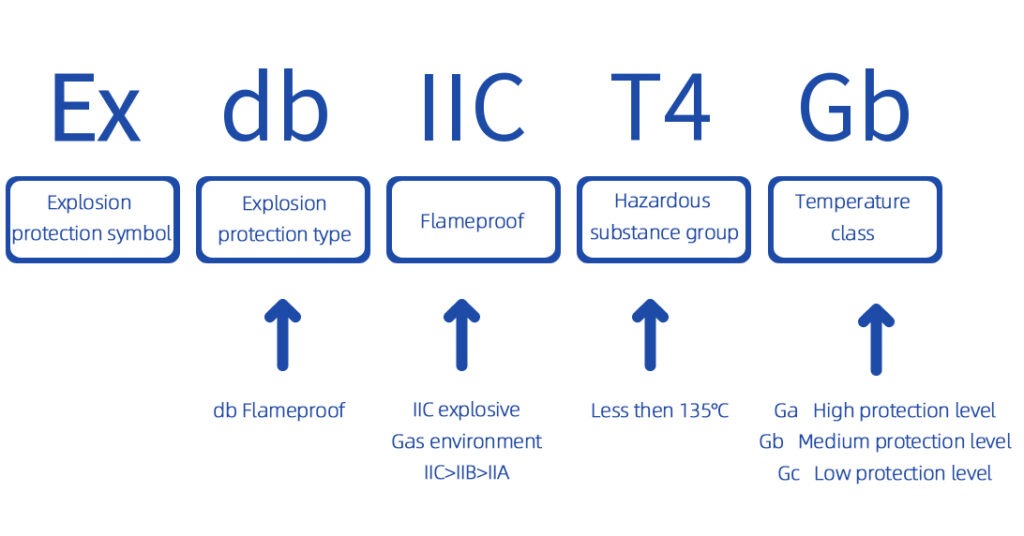
- “Ex”: “Ex,”is abbreviated of “Explosion-proof”, meaning explosion protection. In the standards of China and the International Electrotechnical Commission, “Ex” is the unified marking for explosion-proof electrical equipment.
- “db” Marking for the type of explosion protection: “db” indicates flameproof enclosures, meaning the design of a special flameproof housing confines any potential internal explosions within the enclosure, preventing the explosion flames and products from spreading outward.
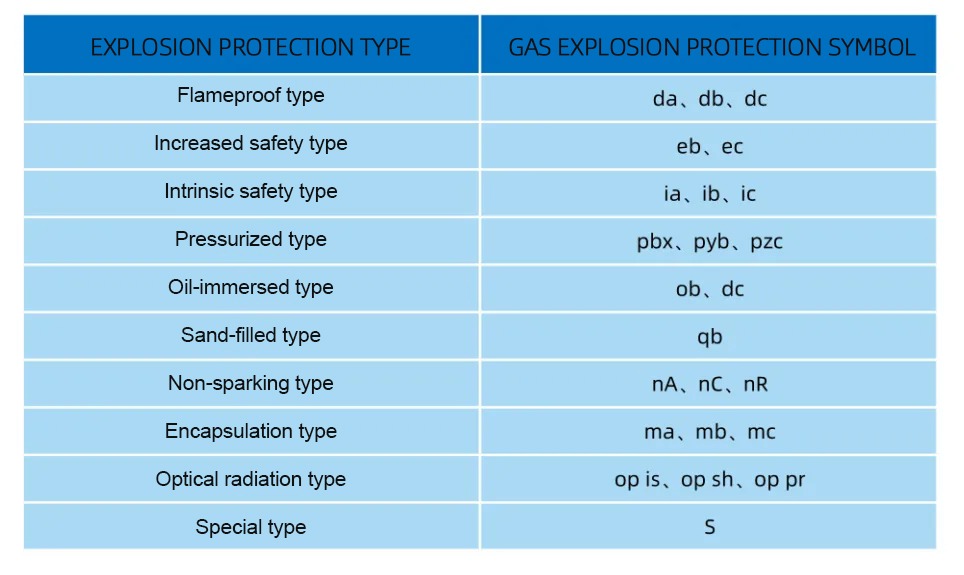
- “IIC” Indicates that the equipment is suitable for IIC explosive gas environments. Since IIC > IIB > IIA, IIC equipment can be used in IIA and IIB environments as well. This means the equipment can safely be used in the most explosive gas environments within these groups.
- “T4” indicates the maximum surface temperature does not exceed 135°C.
- “Gb” denotes the equipment’s explosion protection level for gas.(EPL)
- Ga: High protection level
- Gb: Medium protection level
- Gc: Low protection level
The EF900 series are flameproof products with comprehensive explosion-proof certification.
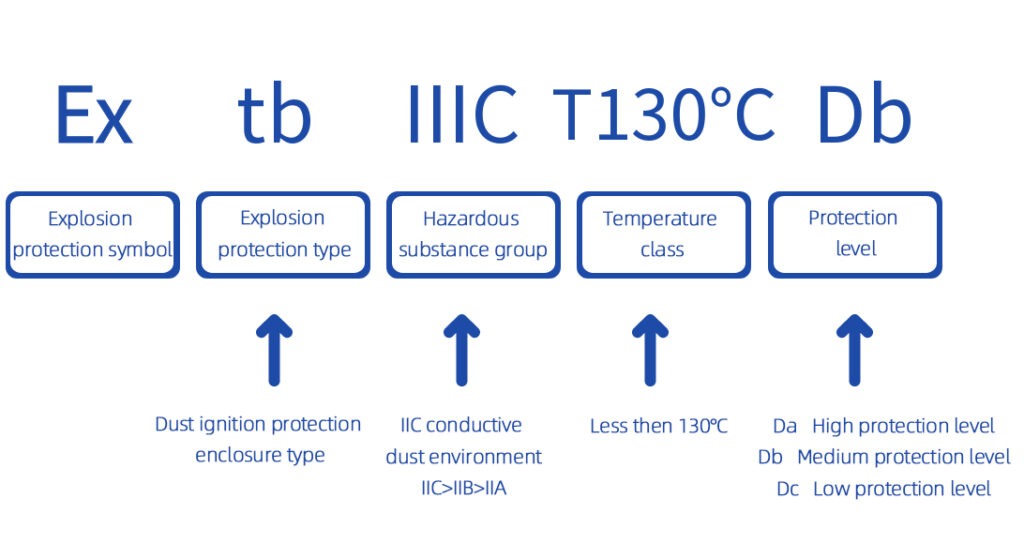
- Ex: Same as above, explosion-proof marking.
- tb: Dust ignition protection enclosure type, meaning the device’s casing can prevent dust from entering and igniting, thereby protecting the safety of the internal equipment and the surrounding environment.
Devices protected by dust ignition protection enclosure “t” are classified as:
ta EPL as Da
tb EPL as Db
tc EPL as Dc
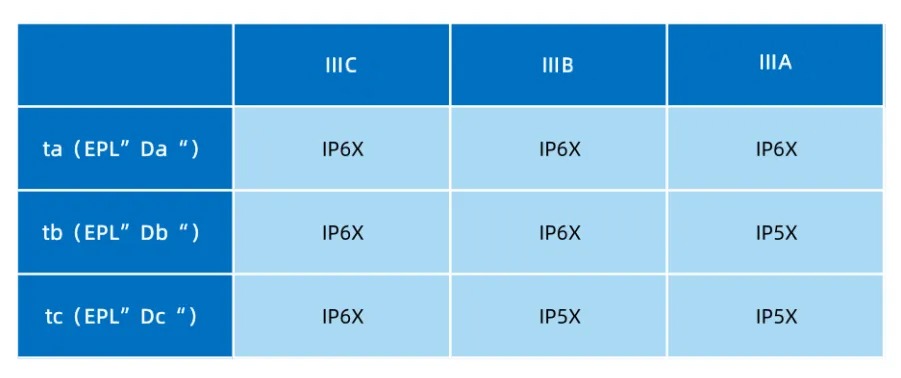
Based on the table from GB/T3836.31-2021 Section 4.2, different protection levels are required to meet specific IP protection standards in various combustible dust environments (Class IIIC, Class IIIB, Class IIIA). The EF900 series has an IP66 protection rating, completely preventing intrusion of solid objects and dust, as well as protecting against strong water jets. This ensures stable operational performance even in harsh environmental conditions.
IIIC: Denotes the device is suitable for conductive dust environments. IIIC can be used in conductive dust environments, which are the most hazardous group in dust environments. IIIC > IIIB > IIIA, so IIIC can also be used in Class IIIA and Class IIIB.
T130℃: Specifies the maximum surface temperature.
Db: Indicates the protection level of the equipment suitable for hazardous areas with combustible dust explosions.
Da: High protection level
Db: Medium protection level
Dc: Low protection level
The EF900 series is a dust explosion-proof product certified for systemic explosion protection. Therefore, the Lead Fluid EF900 series meets both explosion-proof and dust explosion-proof requirements.
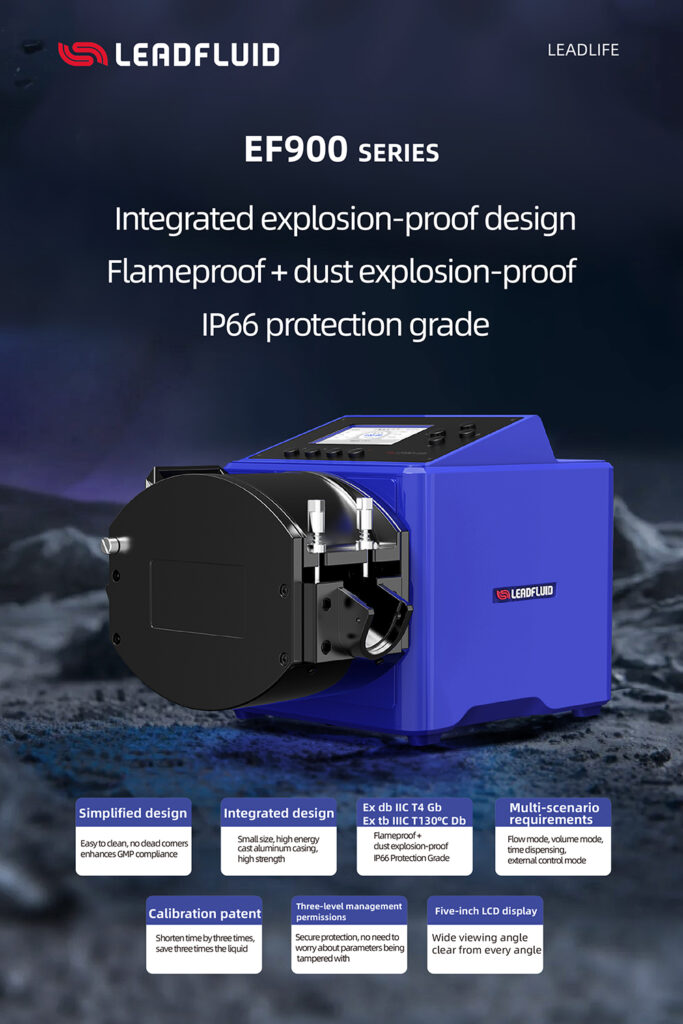
The explosion-proof certificate for the EF800 series, isn’t it easy for everyone to understand?
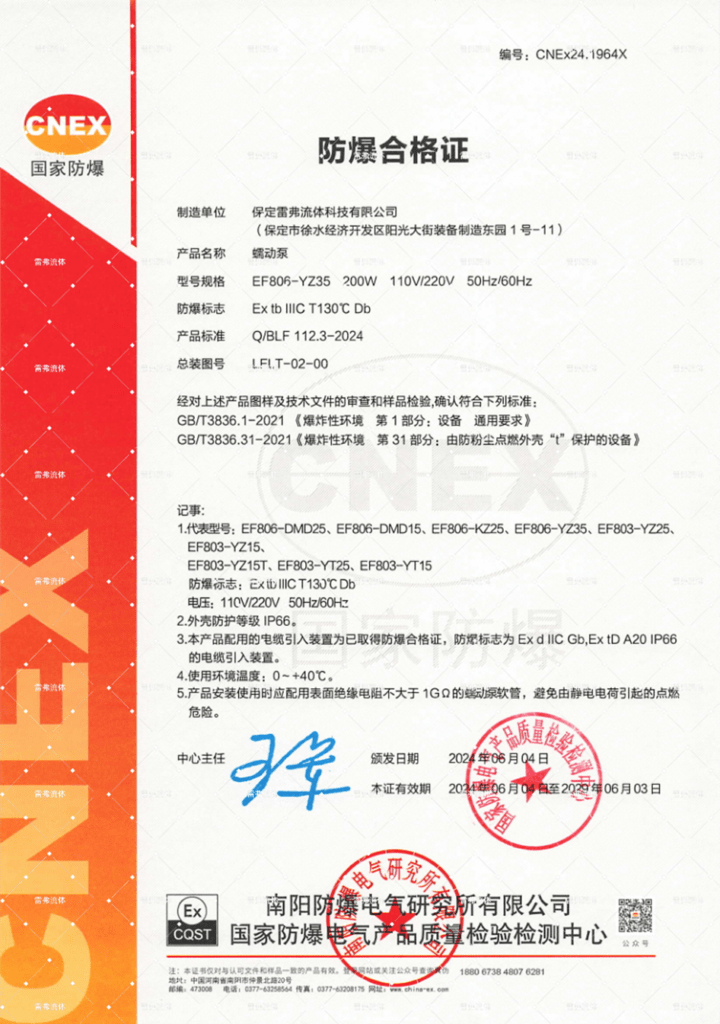

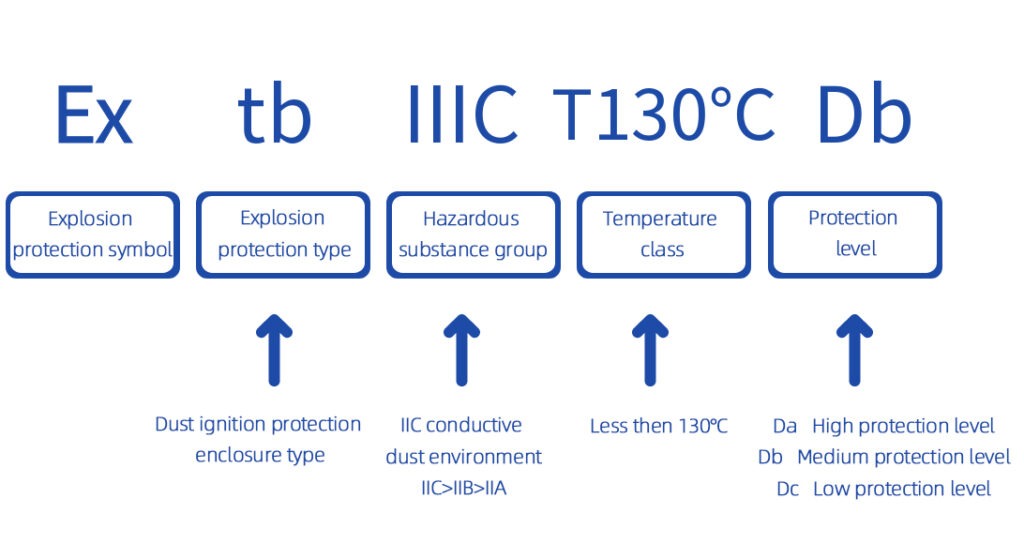
The EF800 series is a dust explosion-proof product certified for systemic explosion protection.
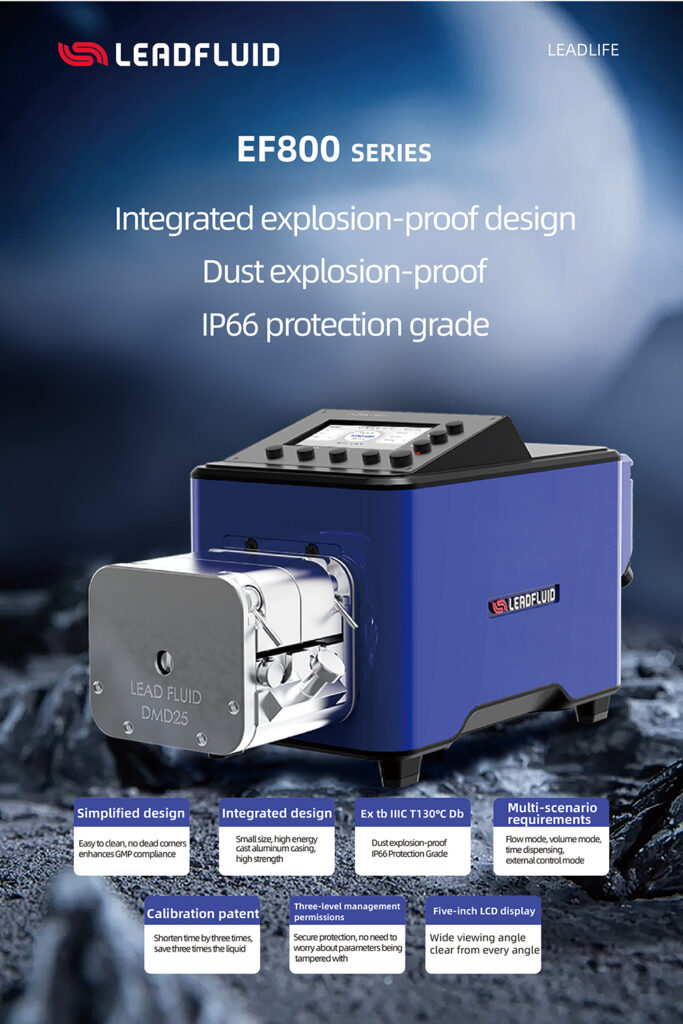
To further deepen everyone’s understanding of explosion-proof knowledge, the next “Lead Fluid Academy” will uncover the differences between the two explosion-proof certifications and share a guide on selecting explosion-proof products.